Geräte zur Bestimmung der Einsatzhärtetiefe EHT / Case Hardness Depth (CHD)
Einsatzhärten
In der Wärmebehandlung spielt die Bestimmung von Härtetiefen eine wichtige Rolle bei der Charakterisierung der Qualität des Wärmebehandlungsprozesses. Bei einsatzgehärteten Werkstücken und Bauteilen wird deren Oberfläche durch Aufkohlen, Härten und anschließendem Anlassen behandelt. Ziel dieser Oberflächenbehandlung ist es, einen weichen und zähen Kern bei gleichzeitig harter Oberfläche zu erhalten. Das Verfahren kommt bei Stählen mit einem Basiskohlenstoffgehalt von weniger als 0,25 Masse % Kohlenstoff zum Einsatz und wird vor allem für Antriebsteile und Zahnräder verwendet. Bei diesen werden die mechanischen Eigenschaften für deren Einsatzzweck verbessert, insbesondere durch:
- einen höheren Widerstand gegen Verschleiß durch erhöhte Randschichthärte,
- stärkere Belastbarkeit,
- bessere Biegewechselfestigkeit und Überlasttoleranz durch den zähen Kern,
- höhere Dauerfestigkeit.
Traditionelle Methode zur Bestimmung der Einsatzhärte
Zur Bestimmung der Einsatzhärte eines Bauteils werden traditionell verschiedene Schritte benötigt, was diese Methode sehr zeitaufwendig macht und die Zerstörung des Werkstücks voraussetzt. Das Werkstück muss geschnitten, geschliffen und poliert werden. Anschließend müssen an mehreren Stellen des Schnittes mit einem Mikrohärteprüfgerät Härteprüfungen vorgenommen werden, um den Härteverlauf zu ermitteln und damit zu bestimmen, ab welcher Tiefe eine definierte Härte unterschritten wird.
Vorteile des HTD
Mit dem HTD können die vorbereitenden Arbeitsschritte eingespart werden. Die Prüfung der Oberflächenhärte erfolgt in einer Messung. Die Kraft-Eindringtiefenkurve wird kontinuierlich aufgezeichnet und die Härtetiefe mit einem speziellen Auswertealgorithmus (Ansatz nach Bückle) bestimmt. Dadurch
- wird die Prüfdauer erheblich reduziert,
- sind keine zusätzlichen Geräte zur Probenvorbereitung notwendig,
- wird das Werkstück nicht zerstört und somit auch Material eingespart,
- können gesamte Produktionschargen in der Serienfertigung effizient geprüft werden.
- Messungen werden nicht durch Krümmung oder Biegung des Werkstückes beeinträchtigt
- Höhere Produktivität
- Zuverlässige Messergebnisse, die nicht vom Bediener beeinflusst werden können (z. B. durch Fehlpositionierung des Werkstückes)
- Durch kundenangepasstes Zubehör können die Prüfungen auch an schwer prüfbaren stellen durchgeführt werden.
- Optimierung der Prozesskontrolle bei der Wärmebehandlung in Echtzeit:
- Überprüfung der Homogenität der Wärmebehandlung
- Schnelle und einfache Einstellung der Ofenparameter
Physikalisches Prinzip der Härtemessung mit dem HTD:
Die Härtemessung basiert auf den folgenden zwei Regeln:
(1) Mindestabstand zwischen zwei Härteeindrücken:
Wenn «d» der Durchmesser des Härteeindrucks ist, so muss der Abstand zwischen
zwei Härteeindrücken für eine gültige Messung mindestens «3d» betragen.
(2) Mindestdicke der Probe:
Wenn «h» die Tiefe des Härteeindrucks darstellt, muss die minimale Probendicke für
eine gültige Messung «10h» betragen.
Beide Regeln basieren auf der Erfahrung, dass das Volumen V2 des an der Bildung des Härtewertes beteiligten Materials viel größer ist, als das Volumen des V1-Abdrucks (V2 >> V1). Der Einfluss des Härteeindrucks geht also weit über seine Größe hinaus (s. Abb. 1).
(1) Mindestabstand zwischen zwei Härteeindrücken:
Wenn «d» der Durchmesser des Härteeindrucks ist, so muss der Abstand zwischen
zwei Härteeindrücken für eine gültige Messung mindestens «3d» betragen.
(2) Mindestdicke der Probe:
Wenn «h» die Tiefe des Härteeindrucks darstellt, muss die minimale Probendicke für
eine gültige Messung «10h» betragen.
Beide Regeln basieren auf der Erfahrung, dass das Volumen V2 des an der Bildung des Härtewertes beteiligten Materials viel größer ist, als das Volumen des V1-Abdrucks (V2 >> V1). Der Einfluss des Härteeindrucks geht also weit über seine Größe hinaus (s. Abb. 1).
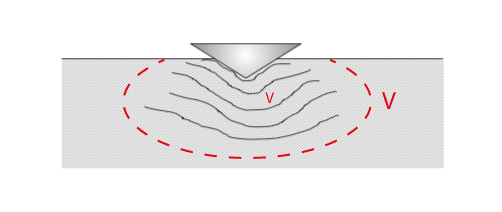
Abb. 1: Auswirkung des Härteeindrucks
Bei einem an der Oberfläche behandelten Material liegt der Eindruck bei kleinen Kräften im Wesentlichen in der harten Oberflächenschicht.
Deshalb wird eine große Härte gemessen. Bei wachsenden Prüfkräften erstreckt sich das an der Bildung des Härtewertes beteiligte Volumen auch in Materialbereiche, die nicht oder nur wenig gehärtet sind (s. Abb. 2).
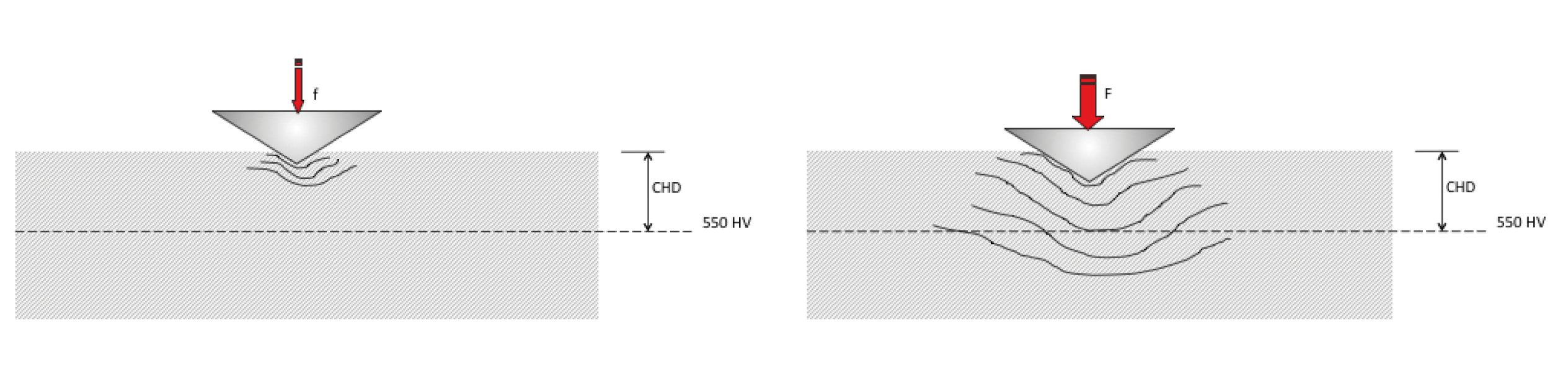
Abb. 2: Eindruck mit niedriger Last führt zu geringer Eindringung (links), Eindruck mit höherer Last führt zu tieferer Eindringung (rechts)
Trägt man in einem solchen Fall die Härte gegen die Prüfkraft auf, so erhält man eine vom Anfangswert der Oberfläche abfallende Kurve (s. Abb. 3).
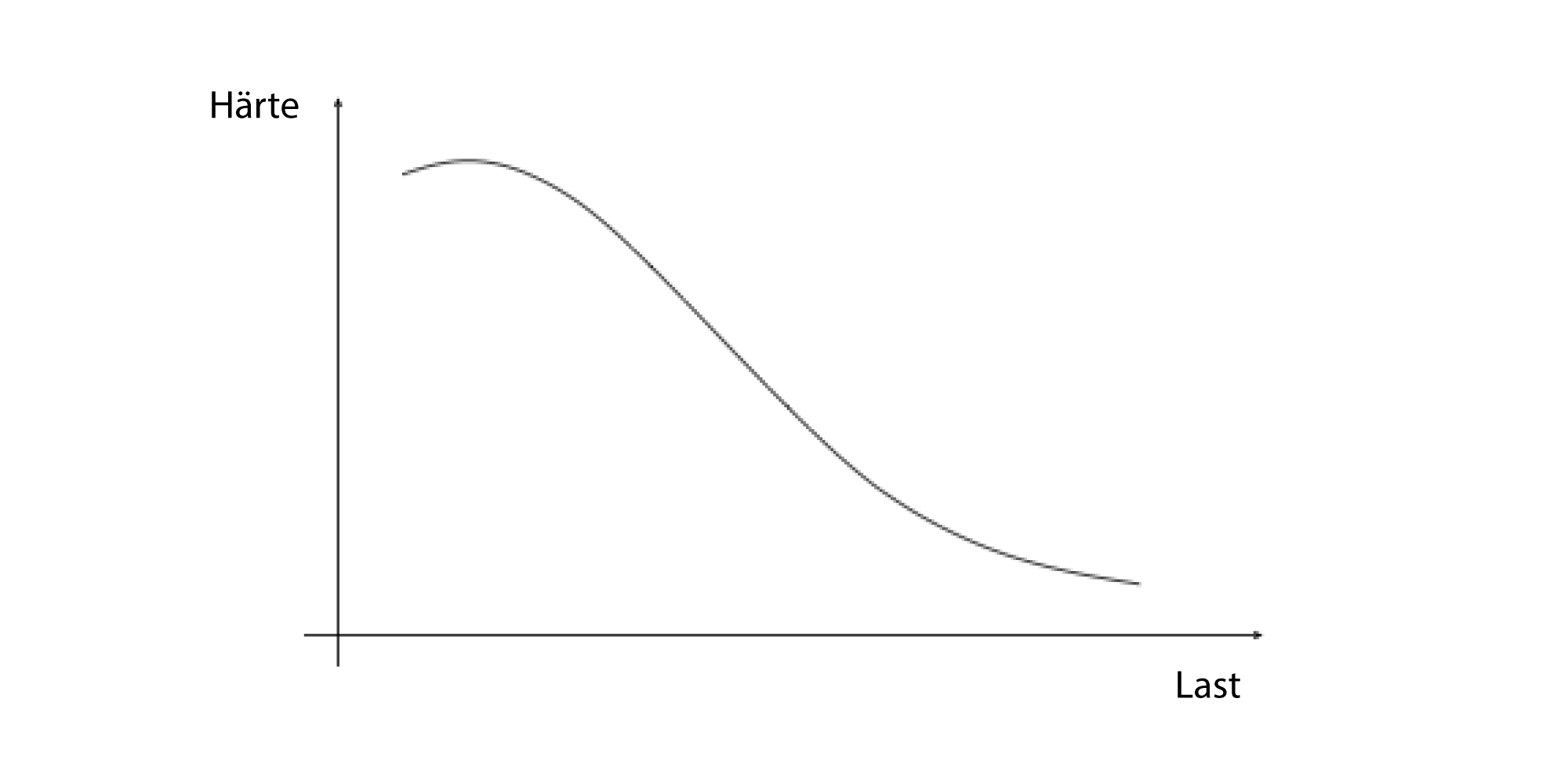
Abb. 3: Kraft-Härte-Kurve
Die HTD liefern für jede Messung diese Kurve.
Die Form dieser Kurve hängt unter anderem auch von der Einsatzhärtetiefe ab und bietet so die Möglichkeit die Einsatzhärtetiefe zu bestimmen.
Mit einem relativ oberflächlichen Eindruck mit dem HTD ist es also möglich die Härte tiefer Schichten zu erfassen, ohne den Eindruck tief setzen zu müssen. Die Auswertung der Kraft-Härte-Kurve erfordert eine quantitative Beschreibung des verformten Volumens.
Bückle hat 1934 einen Ansatz geliefert, der es erlaubt mit einigen Vereinfachungen, den Verlauf der Kraft-Härte-Kurve zu bestimmen. Andererseits kann man aus der KraftHärte-Kurve mit plausiblen, und durch viele Experimente verifizierten Annahmen, die Einsatzhärtetiefe bestimmen.
Die Form dieser Kurve hängt unter anderem auch von der Einsatzhärtetiefe ab und bietet so die Möglichkeit die Einsatzhärtetiefe zu bestimmen.
Mit einem relativ oberflächlichen Eindruck mit dem HTD ist es also möglich die Härte tiefer Schichten zu erfassen, ohne den Eindruck tief setzen zu müssen. Die Auswertung der Kraft-Härte-Kurve erfordert eine quantitative Beschreibung des verformten Volumens.
Bückle hat 1934 einen Ansatz geliefert, der es erlaubt mit einigen Vereinfachungen, den Verlauf der Kraft-Härte-Kurve zu bestimmen. Andererseits kann man aus der KraftHärte-Kurve mit plausiblen, und durch viele Experimente verifizierten Annahmen, die Einsatzhärtetiefe bestimmen.
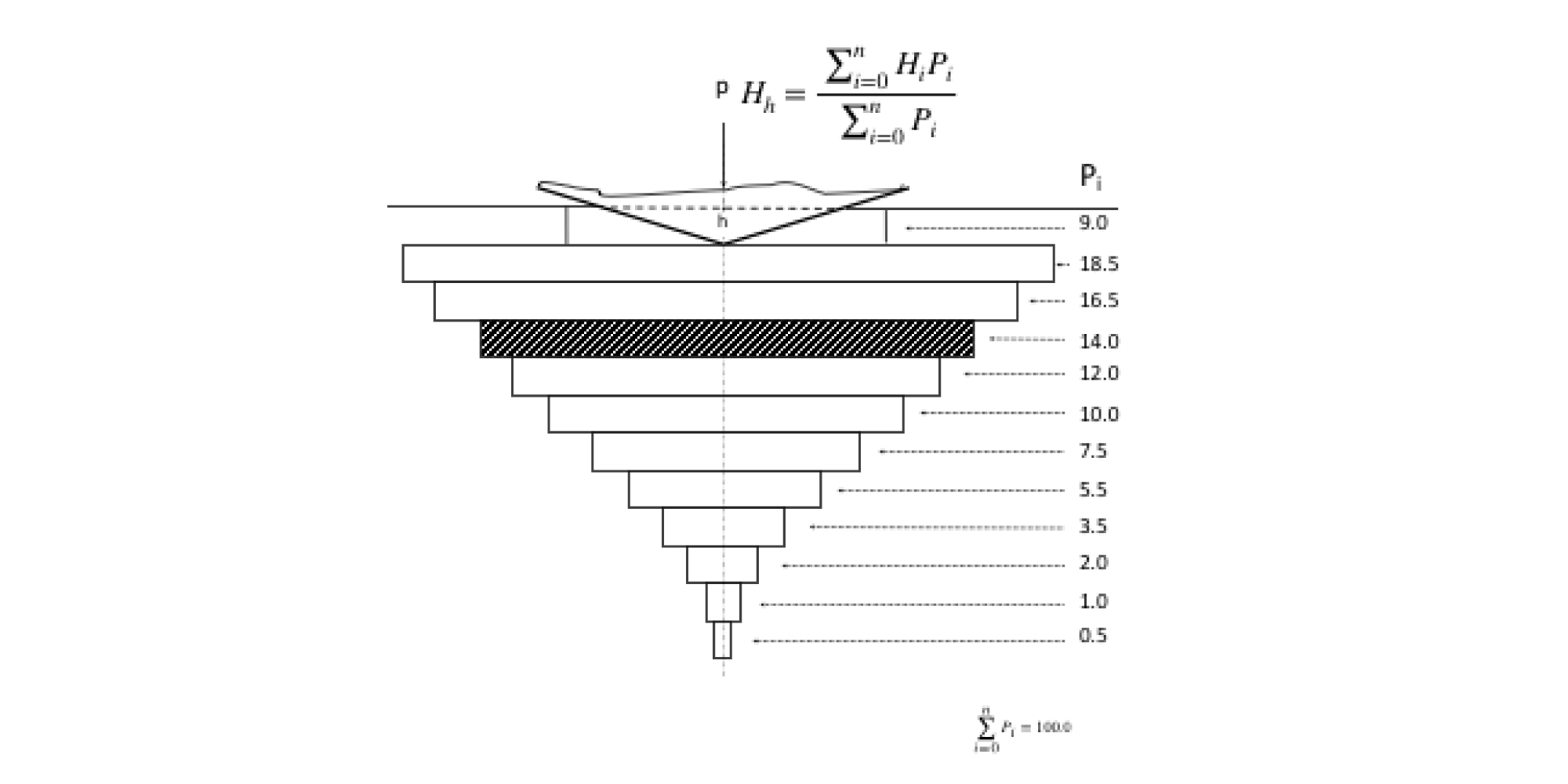